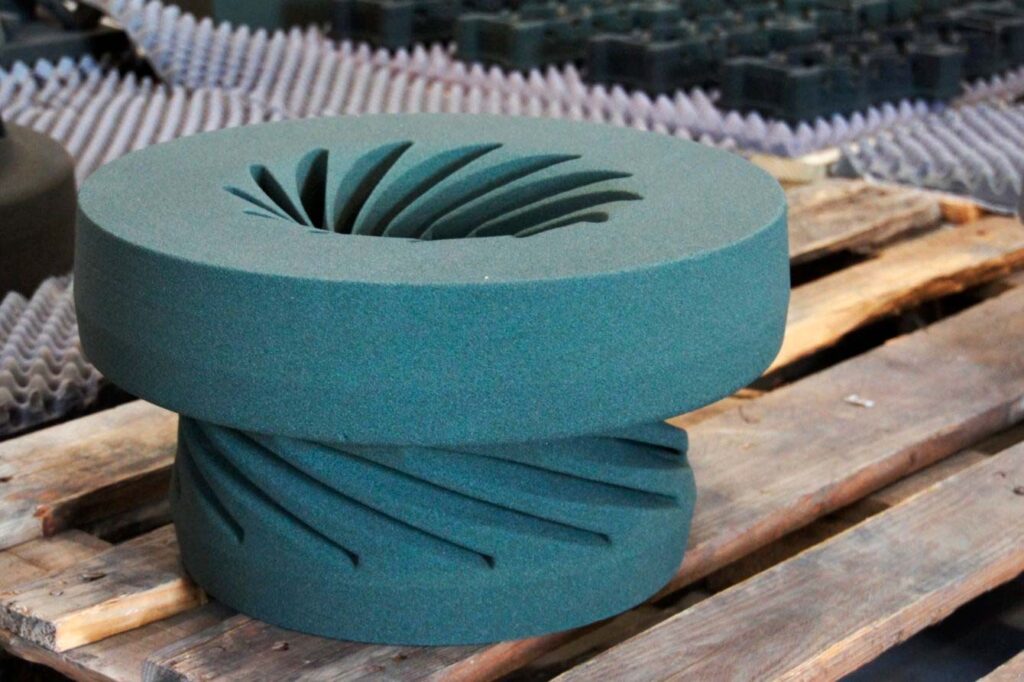
El proceso de moldeo en arena es uno de los métodos más antiguos y versátiles para la fundición de metales. Se utiliza para fabricar piezas metálicas de diferentes tamaños y formas mediante la creación de un molde de arena en el que se vierte el metal fundido. A continuación, se describen los pasos detallados del proceso de moldeo en arena, los tipos de moldes de arena y las ventajas y desventajas del método.
Pasos del Proceso de Moldeo en Arena
Diseño del Modelo:
- Modelo: Crear un modelo (patrón) de la pieza que se desea fundir. El modelo puede estar hecho de madera, metal, plástico u otros materiales.
- Consideraciones de Contracción: Incluir márgenes de contracción para compensar la reducción de volumen del metal al enfriarse.
Preparación de la Arena:
- Arena de Moldeo: Mezclar arena de sílice con un aglutinante (generalmente arcilla bentonítica) y agua para crear la mezcla de arena de moldeo.
- Propiedades: La arena debe tener buena plasticidad, cohesión, refractariedad y permeabilidad para permitir la salida de gases.
Creación del Molde:
- Caja de Moldeo: Colocar el modelo en una caja de moldeo (coquilla) que se divide en dos mitades: cope (parte superior) y drag (parte inferior).
- Relleno: Rellenar la caja de moldeo con la mezcla de arena, compactándola alrededor del modelo.
- Retiro del Modelo: Una vez que la arena está compactada, se retira el modelo, dejando una cavidad en la forma de la pieza a fundir.
Incorporación de los Sistemas de Alimentación:
- Bebederos y Mazarotas: Crear canales de alimentación (bebederos) y reservorios (mazarotas) en la arena para guiar el metal fundido hacia la cavidad del molde y compensar la contracción del metal al solidificarse.
Montaje del Molde:
- Ensamblaje: Ensamblar las mitades cope y drag del molde, asegurándose de que estén correctamente alineadas.
- Colocación de Núcleos: Si la pieza tiene cavidades internas, colocar núcleos de arena en las posiciones correspondientes dentro del molde.
Vertido del Metal:
- Fusión del Metal: Fundir el metal en un horno adecuado hasta alcanzar la temperatura de vertido.
- Vaciado: Verter el metal fundido en la cavidad del molde a través de los canales de alimentación.
Enfriamiento y Solidificación:
- Tiempo de Enfriamiento: Dejar que el metal se enfríe y solidifique completamente dentro del molde.
- Extracción de la Pieza: Una vez solidificado, romper el molde de arena para extraer la pieza fundida.
Limpieza y Acabado:
- Eliminación de Arena: Limpiar cualquier residuo de arena adherido a la pieza mediante vibración, chorro de arena o lavado.
- Desbarbado y Pulido: Quitar las rebabas y realizar el acabado superficial necesario para cumplir con las especificaciones.
Inspección y Control de Calidad:
- Verificación Dimensional: Inspeccionar la pieza para asegurar que cumple con las dimensiones y tolerancias especificadas.
- Ensayos No Destructivos: Realizar pruebas adicionales (como radiografía o ultrasonido) para detectar posibles defectos internos.
Tipos de Moldes de Arena
Moldes de Arena Verde:
- Características: Utilizan una mezcla de arena, arcilla y agua; el nombre «verde» se refiere a la condición húmeda de la mezcla.
- Ventajas: Buena plasticidad, fácil de compactar y moldear.
- Desventajas: Menor resistencia a altas temperaturas y riesgo de deformaciones en piezas grandes.
Moldes de Arena Seca:
- Características: La mezcla de arena se seca o se cura antes del vertido del metal.
- Ventajas: Mayor estabilidad dimensional y resistencia térmica.
- Desventajas: Proceso más largo y costoso debido al tiempo de secado.
Moldes de Arena Química:
- Características: Utilizan resinas sintéticas como aglutinante que se cura mediante reacciones químicas.
- Ventajas: Alta precisión y excelente acabado superficial.
- Desventajas: Mayor costo de los materiales y manejo más complejo de los residuos.
Ventajas y Desventajas del Moldeo en Arena
Ventajas:
- Versatilidad: Adecuado para una amplia gama de metales y tamaños de piezas.
- Costo: Relativamente económico para producciones de baja y media escala.
- Flexibilidad de Diseño: Capacidad para crear formas complejas y detalladas.
Desventajas:
- Acabado Superficial: Generalmente, el acabado superficial es menos fino que en otros métodos de fundición.
- Tolerancias Dimensionales: Menos precisas en comparación con otros procesos como la fundición a cera perdida.
- Tiempo de Producción: Proceso más lento debido a los pasos de preparación, vertido y enfriamiento.
En resumen, el proceso de moldeo en arena es una técnica fundamental en la industria de la fundición que ofrece una combinación de versatilidad y economía, especialmente adecuada para piezas de geometrías complejas y variadas. Con una correcta preparación y control de cada etapa del proceso, se pueden lograr piezas de alta calidad y precisión.